LEAN MANUFACTURING NEL
SETTORE AEROSPAZIALE
L'ESPERIENZA BOEING-ALENIA AERONAVALI
Pietro Antolini
Vi proponiamo un estratto della tesi di Pietro Antolini dal titolo: "Lean manufacturing nel settore aerospaziale". Il lavoro può essere acquistato su Tesionline.
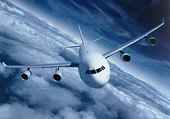
Grandezza caratteri: piccoli | medi | grandi
La difficoltà nel copiare il sistema Toyota
La produzione snella deve essere considerata un vero e proprio modello produttivo originale.
A Toyota servirono decenni di impegno costante e di errori per creare le tecniche e rendere snelli i processi produttivi, di sviluppo prodotto, di gestione dei fornitori, e di tutto quello che ruota intorno ad un grande produttore di automobili.
Non stupisce scoprire quante aziende abbiano fallito nel tentativo di copiarla.
La prima motivazione potrebbe essere la seguente: per decidere di abbracciare completamente questa nuova metodologia, è necessaria una grave crisi che però può spingere a cercare soluzioni a breve termine, non compatibili con un percorso lungo come quello volto a diventare realmente snelli.
Alcuni autori fanno riferimento alla necessità che si formi col tempo una sorta di nazionalizzazione del modello Lean Manufacturing, adatta al paese in cui si opera. Ciò è condivisibile vista anche la portata dei cambiamenti che si generano passando dalla produzione di massa alla produzione snella.
Le chiavi del sistema produttivo Toyota rimangono però i suoi principi più che le sue tecniche. Riconoscendo la superiorità del nuovo modello e l’inevitabilità del cambiamento, si possono trovare centinaia di esempi di altre aziende che sono riuscite lentamente a trasformarsi.
Cosa significa essere snelli - I principi alla base del sistema Toyota
Riconoscendo in Toyota il massimo esempio di Lean Manufacturing, l’analisi dei suoi obiettivi e dei suoi metodi chiarisce quali siano le basi necessarie per la trasformazione.
Per Toyota i due pilastri sono: miglioramento continuo (in giapponese Kaizen) e rispetto per le persone. Il primo necessita del secondo e nessuna azione o decisione può essere presa in contrasto con questi due principi di base.
Questo garantisce la base stabile, una filosofia di lungo periodo.
Sul piano operativo, come dichiarato nel 2005 dal suo presidente Fujio Cho: “La chiave della via Toyota, e ciò che la distingue, non è nessuno dei suoi elementi preso singolarmente. L’importante è avere tutti gli elementi insieme in forma di sistema. Questo deve essere portato avanti giorno per giorno in modo regolare e coerente”.
È interessante, inoltre, notare come Toyota non consideri nessuna delle sue tecniche come essenziale, a differenza di quanto troppo spesso frainteso dai suoi imitatori. Non sono il just in time o il kanban o altre tecniche a costituire il modello Toyota, sono stati l’applicazione assidua dei suoi principi e la creatività nell’approntare nuove soluzioni ai problemi quotidiani della loro integrazione, a portare i risultati visibili oggi.
Si configura quindi un’azienda che, ad un livello più profondo, basa la sua strategia su un sistema in cui tutte le parti devono poter contribuire alla realizzazione dell’obiettivo comune. Per questo forse l’abilità maggiore di Toyota consiste nel coltivare costantemente:
- la leadership
- il lavoro dei gruppi
- la cultura aziendale
- la strategia
- il rapporto coi fornitori
Tutto questo non sarebbe possibile senza che venisse promosso ad ogni livello il concetto di “learning organization” (organizzazione che impara), intesa sia come un’azienda in cui il miglioramento ottenuto si consolida per piccoli passi, ma anche e soprattutto come “evolutionary learning capability” (capacità evolutiva di imparare) cioè un’azienda che impara nuovi modi di rispondere ai cambiamenti.
Cambia quindi la definizione di efficacia, in cui i prodotti non sono più al centro dell’attenzione, e l’obiettivo diventa compiere nel miglior modo possibile qualsiasi azione.
Ohno a tal proposito riporta le parole di Henry Ford:
“La ragione per cui la parola efficacia è così detestata è perché viene pensata come efficienza delle cose. L’efficacia reale consiste invece, semplicemente, nel compiere un lavoro nel modo migliore piuttosto che nel modo peggiore. L’efficacia è trasportare un tronco su una collina usando un camion piuttosto che portarlo sul proprio dorso.”
I concetti fondamentali
Per iniziare quest’analisi si può cominciare con una domanda: perché esiste un’azienda? La risposta ovvia è che essa esiste per soddisfare i bisogni del cliente. La conseguenza, chiave del pensiero snello, è che l’attenzione di tutti deve essere incentrata sulla soddisfazione del cliente, l’obiettivo è fornire al cliente:
- quello che vuole
- quando ne ha necessità
- nella quantità richiesta
- privo di difetti
- al minimo prezzo
Più in generale il cliente potrebbe essere un ufficio o un altro operaio che stanno a valle della catena produttiva e attendono il prodotto per poter compiere le loro azioni.
Per migliorare giorno per giorno il proprio lavoro la prima cosa da fare, secondo il pensiero snello, è individuare esattamente che cosa si debba fare. Una volta che sia chiaro chi è il cliente, il secondo passo è definire le sue necessità. Successivamente è necessario analizzare a fondo le caratteristiche del prodotto per valutare quanto questo risponda alle necessità del cliente. Già a questo punto si potrebbero trovare particolari che non sono nati dalla richiesta del cliente, l’obiettivo è eliminarli. Percorrendo tutta la produzione le attività cosiddette “a valore” risulteranno essere quelle che informano il prodotto, cioè ne modificano le caratteristiche verso quanto richiesto dal cliente.
Questo metodo d’indagine, soprattutto nel caso di prodotti complessi, può risultare difficile, per questo già Ohno aveva definito 7 sprechi fondamentali (in giapponese muda) a cui se ne può aggiungere un ottavo, come suggerito da alcuni autori. Tra i muda abbiamo:
- scorte
- sovrapproduzione
- spostamenti per compiere diverse operazioni
- rilavorazioni dovute a prodotti difettosi
- trasporto di materiali o attrezzature
- inefficienze di processo
- tempo inutilizzato
- creatività inutilizzata
Si potrebbe pensare che questo genere di errori sia raro. Nella pratica se per cliente si immagina un ufficio a valle del proprio a cui si passano diversi tipi di documenti (prodotti), i casi si moltiplicano. La risposta classica potrebbe essere: “questo timbro noi non lo richiediamo, ma se l’ufficio precedente lo mette ci sarà qualcuno a valle che ne ha bisogno…”. Potrebbe invece trattarsi effettivamente di un’operazione inutile. Purtroppo la vicinanza degli uffici non migliora le cose, fin che si mantiene una netta divisione funzionale questo genere di sprechi è destinato a moltiplicarsi.
La maggior parte di questi sprechi rientrano nel senso comune del termine ma alcuni di questi per essere compresi in ottica lean necessitano di spiegazione.
Primo fra tutti le scorte, caratteristica distintiva della produzione di massa, derivanti spesso dalla sovrapproduzione. In questo caso ci si riferisce a qualsiasi genere di scorta: materie prime, semilavorati e prodotti finiti. Tradizionalmente le code di semilavorati sono state sempre accettate e mai particolarmente osteggiate, si possono però riconoscere una serie di problemi legati alle scorte:
- i materiali sono beni immobilizzati che possono avere valore consistente se si considera un intero stabilimento produttivo
- qualsiasi difetto sia presente all’interno di un lotto di semilavorati verrà scoperto dopo diverso tempo con la possibile conseguenza di dover distruggere un intero lotto prodotto in settimane di lavoro o rilavorarlo
- lo stesso difetto, soprattutto se circoscritto ad uno o pochi pezzi genera una conseguenza molto più pericolosa, la mancata identificazione e la sottovalutazione della causa
- non vi è alcun interesse al miglioramento fintanto che permangono grosse scorte a monte e a valle del proprio processo
- la manutenzione o i guasti delle macchine non influiscono sulla produzione finendo per essere accettate come avvenimenti inevitabili
Le scorte assumono quindi un ruolo di “rete di sicurezza” per i processi che tendono a separarsi gli uni dagli altri temporalmente e fisicamente, per la presenza dei magazzini intermedi, finendo per essere completamente indifferenti alle richieste del cliente se non per imposizioni direttive dall’alto. A proposito dello spreco legato alle scorte esiste un aneddoto, avvenuto probabilmente alla Porsche, quando un esperto giapponese si fece accompagnare dal direttore di produzione sulla linea di assemblaggio. Appena entrato esclamò: “Dov’è la fabbrica? Questo è il magazzino!”. Nei giorni seguenti tornò con una sega elettrica e, insieme al direttore di produzione, tagliò a metà tutti gli scaffali.
(L'articolo continua sotto al box in cui ti segnaliamo che alla collana di libri QualitiAmo si è aggiunto un nuovo titolo).
LA COLLANA DEI LIBRI DI QUALITIAMO -
"La nuova ISO 9001:2015 per riorganizzare, finalmente, l'azienda per processi" - Si aggiunge alla collana dei libri di QualitiAmo il primo testo che svela i segreti della futura norma.
Dalla teoria alla pratica: il secondo lavoro di Stefania Cordiani e Paolo Ruffatti spiega come migliorare la vostra organizzazione applicando la nuova norma attraverso i suggerimenti del loro primo libro
(Vai all'articolo che descrive il nuovo libro)"Organizzazione per processi e pensiero snello - Le PMI alla conquista del mercato" - Da una collaborazione nata sulle nostre pagine, un libro per far uscire le PMI dalla crisi.
L’ideatrice di QualitiAmo e una delle sue firme storiche spiegano come usare con efficacia la Qualità.
(Vai all'articolo che descrive il primo libro)
(Vuoi restare aggiornato gratuitamente sulla nuova ISO 9001:2015? Visita ogni giorno la pagina che ti abbiamo linkato.
In calce all'articolo riporteremo quotidianamente un aggiornamento sulla futura norma)
Se questo può far sorridere, un esempio che non può lasciare indifferenti è il percorso tipico dei documenti. Per un impiegato avere una certa coda di documenti in ingresso al proprio ufficio e altrettanti in uscita per l’ufficio successivo, può essere considerata una situazione normale. Se oltre a ciò il numero di documenti da lui processati giornalmente è molto elevato, si considererà sicuramente efficiente e non sarà disposto ad accettare critiche visto l’impegno profuso. Immaginando di essere un cliente in attesa di uno dei documenti nel mucchio la visione diventa subito diversa. Ciò che conta non è più l’efficienza del singolo ufficio, ma il tempo totale per percorrere tutti gli uffici coinvolti. Immaginando poi la presenza di difetti, il tempo necessario a scoprirli e la difficoltà di risalire all’autore, si comincia a comprendere perché le code debbano essere eliminate ad ogni costo da qualsiasi tipo di processo.
(Fonte: Tesionline)
PER SAPERNE DI PIU':
Gli strumenti della Lean manufacturingCome implementare la Produzione snella
Il modello giapponese
Lean manufacturing per accrescere la competitività - L'esperienza Boeing-Alenia Aeronavali
